凿岩台车(隧道及地下工程采用钻爆法施工的凿岩设备)
温馨提示:这篇文章已超过423天没有更新,请注意相关的内容是否还可用!
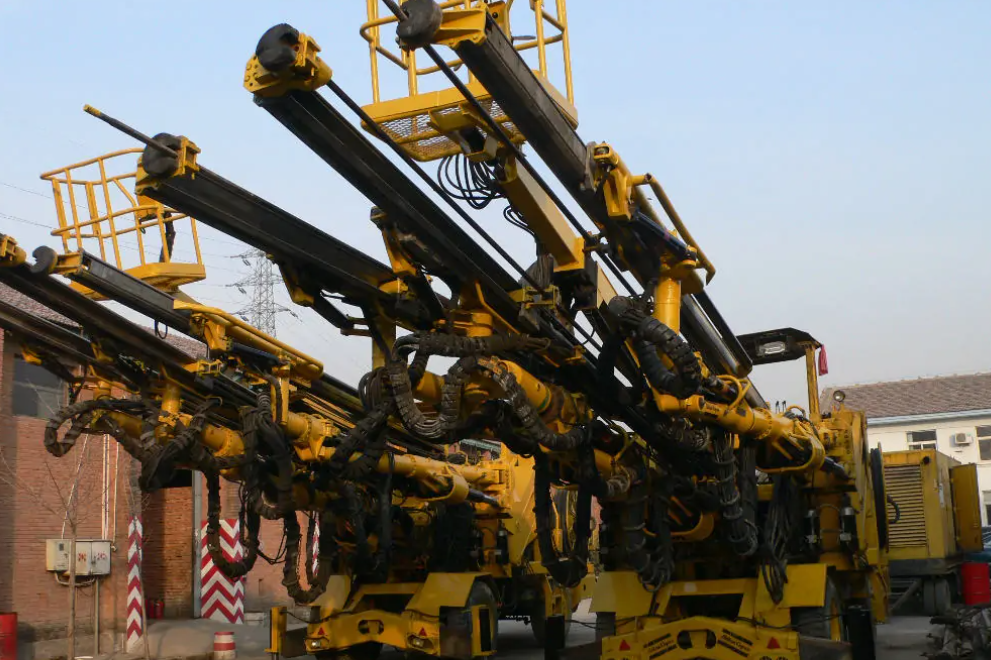
凿岩台车
隧道及地下工程采用钻爆法施工的凿岩设备
凿岩台车(也称钻孔台车)是一种隧道及地下工程采用钻爆法施工的凿岩设备。它能移动并支持多台凿岩机同时进行钻眼作业。
工作机构主要由推进器、钻臂、回转机构、平移机构组成。
台车行走机构有轨道、履带及轮辐式、挖掘式四种。国产凿岩台车以轨道及轮胎式较多。
随着电液比例技术和自动化技术的发展及其在凿岩台车上的应用,全自动化、环保化、多样化是未来凿岩台车的发展趋势。
中文名 | 凿岩台车 |
外文名 | jumbo |
别名 | 钻孔台车 |
组成 | 凿岩机、钻臂 |
领域 | 能源 |
学科 | 矿业、机械 |
简介
主要由凿岩机、钻臂(凿岩机的承托、定位和推进机构)、钢结构的车架、走行机构以及其他必要的附属设备,和根据工程需要添加的设备所组成。应用钻爆法开挖隧道时,为凿岩台车提供了有利的使用条件,凿岩台车和装碴设备的组合可加快施工速度、提高劳动生产率,并改善劳动条件。
将一台或几台凿岩机连同自动推进器一起安装在特制的钻臂或钻架上,并配以行走机构,使凿岩作业实现机械化。
凿岩钻车可分为平巷掘进钻车、采矿钻车、锚杆钻车和露天开采用凿岩钻车等;按照钻车的行走机构可分为轨轮、轮胎和履带式;按照架设凿岩机台数可分为单机、双机和多机钻车。
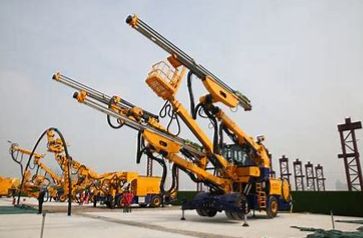
发展现状
国外凿岩台车的研究及发展现状
国外研制液压凿岩机始于20世纪70年代,先后有美国Ingersoll2Rand公司、Gardner2Denver公司、瑞典AtlasCopco公司、Linden2Alimak公司、芬兰Tamrock公司、法国Eimco2Secoma公司、德国Krupp公司和日本古河(FURUKAWA)公司等投入力量研制液压凿岩机及相关配套钻车。其中瑞典AtlasCopco公司和芬兰Tamrock公司生产的液压凿岩机及配套钻车最具代表性,占有60%以上的市场份额。截止2009,无论是井下或露天掘进或采矿,都有相应的液压凿岩机供选用。如芬兰Tamrock公司80年代初液压凿岩机只有3个系列,2009该公司的产品已发展到7个系列,从小型手持式到超重型,品种规格齐全。在发展回转-冲击式产品的同时,适用于软岩上钻孔的纯回转液压凿岩机也得到相应的发展。尤其是瑞典AtlasCopco公司能够灵活地根据用户的某些特殊要求,在某种基型产品上稍加改进,就可以组装成专用产品,产品上的配套部件可随不同地区和国家的不同环境而改变,在轻型产品的研制中,大量采用塑料件来减轻整机的重量。液压凿岩机的外壳等多采用精密铸造,从而使机器的结构紧凑,布局合理,外形也较美观。
如今AtlasCopco公司生产的Cop系列液压凿岩机已经从Cop1022发展到最新推出的Cop4050型重型液压凿岩机,Cop4050的冲击功率可达40kW,装配于Simba4450系列全液压钻车上,1993年成功用于瑞典卢基公司基律纳铁矿井下深孔采矿凿岩,钻凿孔径达115mm,这是传统的潜孔冲击器的工作范围。潜孔凿岩虽然能得到较好的孔直度,但速度较低。Cop4050能在两倍于潜孔凿岩速度的情况下,得到几乎全直的孔,并能使用通常的钻管、钎杆或二者的组合。Tamrock公司生产的HL4000系列大功率超重型液压凿岩机,1984年在挪威年产2500万t的比约纳湖(Bjornevatn)铁矿装配Herbert钻车用于露天矿山钻凿直径230~275mm的炮孔,其凿速相当于同级牙轮钻机的116倍,而能耗仅为牙轮钻机的1/2。由于液压凿岩机具有节能、高效、成本低和作业条件好等显著优点,国外除地下凿岩已推广应用外,在中小型露天矿和岩石工程应用方面也有不小进展。
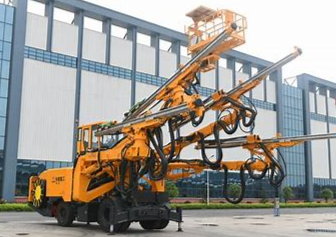
国内凿岩台车的研究及发展现状
1980年由长沙矿冶研究院、株洲东方工具厂等单位研制成功我国第一台用于生产的液压凿岩机YYG80,装配于CGJ2Y型全液压钻车上在湘东钨矿进行了工业试验并通过了部级技术鉴定。由此拉开了国内研制液压凿岩机的序幕。相继有北京科技大学、中南工业大学、长沙矿冶研究院、马鞍山矿山研究院、中国矿业大学、煤炭科学院建井研究所、沈阳风动工具厂、天水风动工具厂、衢州凿岩机厂和宣化风动工具等10多个单位开发研制液压凿岩机和配套钻车,到了九十年代末期,我国先后有YYG80、TYYG20、YYGJ145(仿Cop1038H)、YYT30、YYG30、GGT70、YYG80A、YYG90、YYG250A、CYY20(仿法国RPH200)、YYG90A和DZYG38B(仿Cop1238ME)等十二种机型通过了国家鉴定。其中冲击能在150J以下的5种,其余的7种冲击能均在150~250J之间。可钻孔径大部分在40~50mm之间,只有YYG250A、YYGJ145、TYYG20和DZYG38B型液压凿岩机可钻孔径大于50mm,最大可达120mm。其中已形成量产的主要有YYG80、YYT30和YYG90A三种机型。12种型号中除3种为测绘仿制国外当时市场销售的机型外,其余都是我国自行研制的。
由中南工业大学研究设计,广东有色冶金机械厂制造的CGJ25-2Y型全液压钻车,装配两台YYG90型液压凿岩机,,1988年在汝城钨矿使用时,与铲插式装岩机、搭接式梭车组成掘进机械化作业线,创造了在214m×216m断面中月进尺250m,掘进工效稳步超过1m/工班的好成绩,1991年在桓仁铜锌矿创造过单台单班进尺514~6m的好成绩。
与法国水星系列液压钻车配套的HYD200和HYD300液压凿岩机由莲花山有色冶金机械厂引进法国Eimco2Secoma公司技术生产,其国产化率已达95%,主要部件冲击活塞寿命可达2万m以上,各项指标均已达到国外同类机型的水平,已形成批量生产。
天水风动工具厂生产的CTJY12-3型全液压轮胎式掘井钻车配置三台YYGJ145型大功率液压凿岩机、三个AB741型液压钻臂、AT1541型液压推进器及一个AF321型液压工作平台,是我国最大的具有80年代世界先进水平的地下掘进钻车。
从上述可以看出,我国液压凿岩机的发展走的是一条自主研发与引进消化国外技术相结合的道路,经过几十年的发展与探索已经初步形成了自己的产品规格与系列,达到了一定水平。但大多数厂家生产的液压凿岩机稳定性指标均在500m左右(不拆机检修),而世界先进水平的瑞典产品则规定为6000m。国内只有中国地质大学生产的DZYG38B型液压凿岩机样机的工业性试验才达到这一世界水平的指标。因此,国内液压凿岩机与国际先进水平尚存在很大差距,引进机型尚未完全国产化,其关键零部件仍依赖进口。究其原因主要有如下几个问题:一是高速、高压下的密封结构和支承活塞运动的前、后导向套的结构;二是活塞、钎尾、导向套和密封材料的选择与应用,以及材料热处理和高精度加工;三是蓄能器隔膜的材料及寿命等。从而导致零件寿命低,密封不可靠,内外泄漏严重,以及活塞研缸和导向套咬合等故障,造成国产液压凿岩机可靠性指标下降。
根据平巷掘进作业和钻孔布置的要求,以CGJ-2Y型全液压凿岩钻车为例,来说明凿岩钻车必须具备的主要组成部分和它们的工作原理。凿岩钻车钻臂8的运动方式为直角坐标式。利用摆臂油缸12可使转柱套及铰接在其上的钻臂8与支臂油缸19绕转柱10的轴线左右摆动;利用支臂油缸可使钻臂绕铰点上下摆动,从而使用托架5铰接在钻臂前端的推进器4作上下左右的摆动。推进器亦可借助俯仰油缸20和摆角油缸6作俯仰和左右摆动运动。推进器可使安装在推进器滑架上的液压凿岩机前进或后退。凿岩时,推进器将给凿岩机以足够的推进力。借助由支臂油缸、推进器俯仰角油缸和摆角油缸以及相应的液压控制系统等组成的液压平移机构,可以获得相互平行的钻孔。单独控制俯仰油缸和摆角油缸时,可钻凿具有一定角度的倾斜孔。通过翻转油缸使推进器绕油缸的轴心线翻转,以便获得靠近巷道两侧和底部的钻孔。由于上述各机构的相互配合,即可在巷道断面内的任何部位钻凿各种方向的钻孔。在推进器的前方安有钎杆托架2和顶尖3,借以保持推进器工作时的稳定性。补偿油缸7可使顶尖始终与工作面保持接触。在钻车车体上还布置着油箱与油泵站、操纵台、车架与行走装置、以及液压、供电、供水、供气等系统。为使车体在工作时保持平衡与稳定,在车体上还装有前后支腿18与15。
工作机构
工作机构主要由推进器、钻臂、回转机构、平移机构组成。
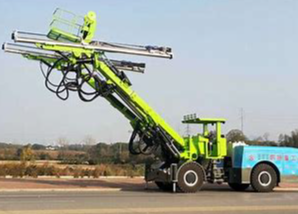
推进器
主要有钢绳活塞式、风马达活塞式、气动螺旋副式。推进器的作用是:在准备开孔时,使凿岩机能迅速地驶向(或退离)工作面,并在凿岩时给凿岩机以一定的轴推力。推进器的运转应是可逆的。推进器产生的轴推力和推进速度应能任意调节,以便使凿岩机在最优轴推力状态下工作。
钻臂
钻臂是支撑凿岩机的工作臂。钻臂的结构和尺寸、钻臂动作的灵活性和可靠性等,都将影响钻车的适用范围及其生产能力。
按照钻臂的动作原理:有直角坐标、极坐标和复合坐标三种。
直角坐标钻臂具有钻臂的升降和水平摆动、托架(推进器)的俯仰和水平摆动及推进器的补偿运动等基本动作。这些动作分别由支臂油缸19、摆臂油缸12、俯仰角油缸20、托架摆角油缸6和补偿油缸7来实现。
回转机构
回转机构主要可分为:摆动式转柱、螺旋副式转柱、极坐标钻臂回转机构几种。
摆动式转柱的结构特点是在转柱轴3外面有一个可转动的转套2。钻臂下端部和支臂油缸下铰分别铰接于转动套上。当摆臂油缸1伸缩时,使转动套绕轴线转动,从而带动钻臂左右摆动。摆动式转柱结构简单、工作可靠维修方便。
推进器平移机构
在钻车中常用的平移机构有机械式平移机构和液压平移机构两大类。属于机械式平移机构的有:剪式、平面四连杆式和空间四连杆式等几种;属于液压平移机构的有无平移引导缸式和有平移引导缸式等。
分类
台车行走机构有轨道、履带及轮辐式、挖掘式四种。国产凿岩台车以轨道及轮胎式较多。
轨行式台车
车体一般为门架式,故常称门架式凿岩台车。其上部有2~3层工作平台,能安装多台(可达21台)凿岩机;下部能通过装碴机、运输车辆及其他机具。这种台车具有钻眼、装药、支护、量测等多种功能。它是为了适应大断面隧道施工的需要,同时克服手持式凿岩机钻眼效率低的缺点而发展起来的,在铁路隧道和水工隧洞施工中被推广应用。在车体上安装数个钻臂(用以安装凿岩机,一般1~4台)的可自行的凿岩机械设备。钻臂能任意转向,可将凿岩机运行至工作面上任意位置和方向钻眼(孔)。钻眼(孔)参数更为准确、钻进效率高、劳动环境大大改善。
台车动力分机械式和液压式,后者应用较多,自动化程度高,整个钻眼(孔)程序由电脑控制。在发展过程中,起初采用风动凿岩机的梯架式凿岩台车,逐步为用液压凿岩机的门架式凿岩台车所代替。
轮胎履带
主要由柴油机驱动,安装2~6台高速凿岩机,车体转弯半径小,机动灵活,效率高,一般用于矿山平巷掘进,也可用于隧道及地下工程的开挖。
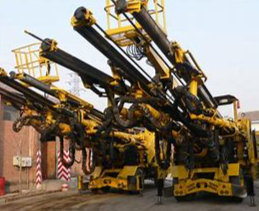
应用
中国京广铁路大瑶山双线隧道施工中,采用的四臂液压凿岩台车,为柴油驱动的特种载重汽车,由气控液压操纵,台车全长15米,高4.3米,宽3.5米,重42吨,配备有液压凿岩机4台,其钻凿速度一般比风动的高50~100%,能量消耗为风动的三分之一,且可减少噪声;还能根据围岩硬度调整油量、压力和活塞冲程,提高凿岩功效。随着喷锚支护技术的发展,扩大了全断面一次开挖的应用范围,为凿岩台车提供了有利的使用条件,新型液压凿岩机的问世,并用于凿岩台车上,将使整个隧道及地下工程转向全液压大型机械化施工的新阶段。
故障分析
前期故障
前期故障,即由于设计不周密等引起的故障,主要反映在以下几个方面:
1、新车无法定位
新车刚到位时,钻臂端千斤顶支腿控制采用左端横向纵向联动,右端横向和纵向联动,联动的支腿油缸同时伸出同时缩回。这样,定位时,当纵向支腿触地后,系统压力油通过安全阀卸压回油,定位操作被迫中止。将联动方式改为:左右端的横向联动和左右端的纵向联动,或者改变联动控制为单独控制,凿岩台车都可以实现定位。
2、安全阀灵敏度不高,引起故障
定位系统钻臂端千斤顶支腿可纵向伸缩,也可横向伸缩,正确的定位方法是:钻孔前先横向伸出,后纵向伸出,钻孔完成后,先纵向缩回后横向缩回。如果操作顺序有误,由于定位系统所依的安全阀灵敏度不高,就会使得定位压力骤增时,出现使用初期的“定位爆管、漏油”等故障,既浪费,又耽误隧道作业时间。
3、误操作引起的故障
虽然定位泵停止了工作,但定位系统仍有压力,如果误碰或误操作控制手柄,将可能产生故障,甚至造成事故。只要对液压系统进行适当改进,就可实现误操作过载保护,在爆管前泄油,定位系统得到保护,并可提高台车钻孔时定位系统的可靠性,消除事故隐患。
4、压力油路过滤系统不完善引起的故障
由于NH178凿岩台车压力油路过滤系统的原理是当过滤器堵塞时,压力油不回油箱,而是继续进入系统。这样就很容易引起系统失控,使用初期常出现的推进油缸失控就是这个原因。对压力油路过滤系统改进即可减少系统失控故障。
使用性故障
使用性故障就是使用过程中不熟悉设备的工作原理,使用不当,设备常常带病工作,使得设备长期失去许多应有的安全保护措施,智能控制功能不完善引起的故障。故障出现后,对设备损害很大,常见的使用性故障有:
1、水路引起的故障
蓄水池等水源不干净,机内水滤网就会堵塞破损,如不及时检查更换,砂石进入后会引起增压水泵叶片打碎或加速磨损,这样,工作水压下降,水控气阀打不开,全车气路控制部分不能工作。如果想继续工作,就必须改变气路,拔掉N8气管,使得气路不受水压控制,台车低水压工作。由于水控气阀不动作,断水时就不能停钻,必然发生卡钎,旋转马达受阻,油压急剧升高,这时,防卡钎阀再不动作,就不能泄压回油,定会发生钻杆钻头卡死,液压油管破裂,系统漏油或油温升高现象。水路中,液压油散热器循环不良也会引起油温高。
2、压力表损环引起的故障
九路压力表分别对三个臂的防卡钎压力、定位压力、推进返回压力起着监测作用,三个冲击压力表可以监测三个臂的冲击压力,如果这些压力表损坏后不及时更换,就会出现下述问题:(1)由于液压元件磨损,压力油泄漏,使得液压系统失去控制,不能正常工作;(2)或者为了工作盲目调高压力,就会经常出现油管爆裂、漏油。在现场发现:三个臂的推进压力为正常压力的1.2-1.5倍;三个臂的推进返回压力为正常压力的2-2.5倍;三个臂的冲击压力也偏高;防卡钎没能协调工作,初卡钎时不返回,经常爆管、漏油,这些都是压力表损坏后,调高压力,勉强工作造成的故障。同时,这也是钻头、钻杆超耗的原因之一。
3、回油系统故障
回油过滤器在回油系统中起过滤杂质和散热冷却作用。回油过滤器的工作情况通过感应器传到配电柜的报警电路,回油警示灯亮时,提示更换回油过滤器。如果由于感应器损坏,又不及时更换,回油过滤器的工作情况就会恶化。首先是堵塞引起回油压力增高、散热差,再不更换回油过滤器,就会引发液压元件磨损泄漏,液压管路爆裂。
4、电路引起的故障
凿岩台车采用高压供电,低压控制。电路出现故障后勉强工作就会失去平衡,电器元件发热间接影响液压油温,如充电器损坏不修理就会引起控制变压器发热,而脉冲发生器损坏就会引起润滑油不工作,磨损凿岩机,引起漏油、升温。
5、油料选用不当引起的液压系统故障
液压油、液压油管在凿岩台车的使用中,对凿岩台车的性能影响非常大。如果不按标号、特性选用合格的液压油,那么液压油的机械杂质含量就偏高、含有水分、抗磨性不好;如果选用的液压油管是伪劣产品,特别是超过保质期的积压产品,使用时就会出现内层脱落,有的接头加工粗糙,残屑就会进入液压系统;这些都会引起油路不畅,造成油缸、马达早期磨损,液压阀堵塞或磨损,最终导致内泄外漏,压力不足,控制失灵,要想工作只能是调高压力,强制钻孔,为液压系统埋下故障隐患。
同时,液压系统在组装时带入系统的固有杂质,及使用过程中产生的氧化物和维修装配时外界侵入的粉尘、水、空气等污染物都会直接或间接引起各种故障,只要加强系统的污染控制,保持系统清洁,就会减少和避免故障发生。
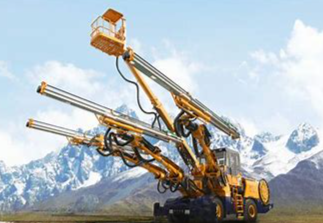
发展趋势
随着电液比例技术和自动化技术的发展及其在凿岩台车上的应用,凿岩台车呈现出从机械化向自动化、环保化、多样化发展的趋势。
凿岩台车的全自动化发展趋势
随着液压控制和电子技术的发展和应用,凿岩循环已实现自动化,即自动开孔、防卡钎、自动停机、自动退钎、台车和钻臂自动移位、定位以及遥控操作系统等。全自动化的台车被称为凿岩机器人。由于这类凿岩机器人主要用于隧道的开挖,又被称为隧道凿岩机器人。挪威、日本、法国、美国、英国、德国、芬兰、瑞典及俄罗斯等国家的多家企业相继参与了全自动化凿岩机的研制工作。特别是近年来,液压控制技术和计算机技术的结合更促进了凿岩技术的进步,自动化凿岩及自动凿岩台车也相继出现,并已达到实用化的程度。
凿岩台车的环保化发展趋势
为了降低噪声,保护操作人员的健康和改善工作环境,一般选用液压凿岩机。这是因为液压凿岩机噪声小,不会排出油雾和有害气体。与气动凿岩机相比,液压凿岩机还具有动力消耗少、能量利率高、凿岩效率高、没有排气噪声等优点。但是,液压凿岩机产生的噪声声压级仍高于90dB(A),达到100dB(A)左右,且声能主要集中于1kHz一5kHz频率段,仍在人耳敏感频率范围内。若不采取噪声防护措施,对施工人员的身体健康仍然有害。液压凿岩机的噪声源主要有冲击机构产生的噪声、回转机构产生的噪声和钎头破碎岩石产生的噪声。液压凿岩机的噪声主要由结构噪声引起,液压凿岩机结构间隙、蓄能器参数、撞击材料的特性以及连接件的松紧度等都是影响液压凿岩机噪声的因素。要降低液压凿岩台车的噪声,应综合采取多种措施。研究人员除了对液压凿岩机结构进行技术攻关、技术改造外,还在远距离有线无线控制和设计研制全隔音驾驶室等方面取得了很大突破。
凿岩台车的多样化发展趋势
2009年世界上各大公司液压凿岩台车的钻臂、推进器和操纵系统等主要部件都已实现标准化和系列化。适用范围广,零件通用率高,可根据用户的不同要求组装成各种型式的台车,实现了品种的多样化,同时缩短了产品设计周期,产品更新换代快。
国外大型台车有定型和非定型两类。定型台车的工作断面规格、钻臂及其布置、凿岩机、推进器配套规格,钻臂安装基座构件型式、钻车底盘等均是定型的。当定型钻车不能适应工程要求(主要是工作断面、凿岩生产率和臂数不足)时,则采用专门设计的非定型钻车。它的主要工作部件如钻臂、凿岩机、推进器等与定型钻车是通用的,不同之处在于根据用户对掘进尺寸、形状、掘进速度等不同的要求选配钻臂数、钻臂在断面的布置、安装基座构件型式、底盘型式、举升工作平面数量、液压系统等。
另外为了适应各种施工的需要,凿岩台车还向着大型化和小型化的方向发展。
参考资料
1.凿岩台车的研发情况与发展趋势·知网
2.凿岩台车全断面快速掘进技术·知网
3.对液压凿岩台车在隧道施工中推广应用问题的浅析·知网